Matching A/D Converter Performance With Application (Part 4)
A fundamental understanding of precision and accuracy and how they relate to ADC specifications enable the designer to quickly choose the right ADC quickly for their application.
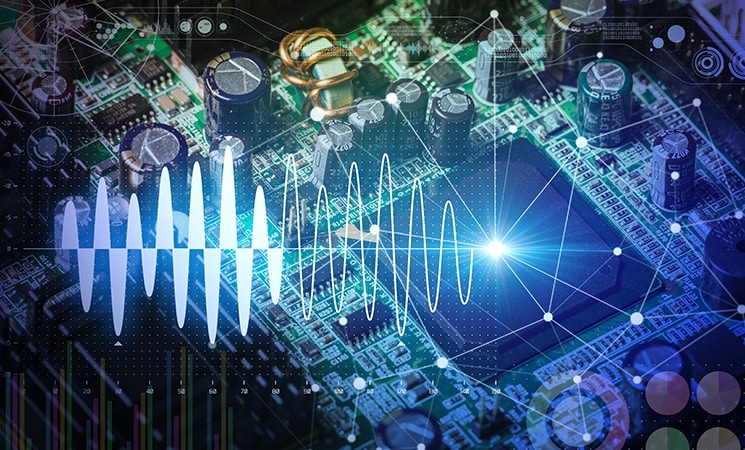
In part one of the article series, we described a customer problem. They were not getting the accuracy they expected in their system even though they thought they selected an appropriate level of performance in their ADC. In part two we defined the ADC parameters that affect precision and accuracy. In part three we looked at four contributing factors that explain how and why ADC parameters vary.
In part four we will look at how the four contributing factors led to decreased system performance and ultimately their high reject rate.
The four contributing factors that led to compromises in ADC performance are: integration and test capability, temperature variation, and process technology.
Integration and Test Capability
Since the device that the customer was using was primarily digital, digital test capability was prioritized over analog test capability. This makes sense from an efficiency and cost perspective, but it compromises analog performance.
When an analog parameter is “guaranteed by design” or “guaranteed through characterization”, it means either no data is taken, or a very limited amount of data is taken to guarantee the parameter. What happens when a manufacturing process shift occurs or a change in the manufacturing material set occurs? There could be a shift in parameters that may deviate significantly from the published data sheet value. If there is no testing of analog parameters, then the device performance will no longer match the published data sheet parameters. This could lead to system level performance issues.
Even if the device is characterized, it may be done on a limited number of devices under a given condition. The problem is that the customer in the example needed precision and accuracy for all devices over all conditions. This is extremely important since many sensors are non-linear over temperature and applied load. Furthermore, many quality engineers have been plagued with quality and reliability issues with analog devices, not because they don’t meet parametric specifications, but because they have so much variation from device to device or lot to lot.
Temperature Variation
The fact that the integrated ADC did not specify changes in DC specifications over temperature led the customer to ignore these sources of error. Not only were there temperature effects as the integrated ADC heated up, but there were also temperature effects from the test floor and the test equipment increasing the temperature of the board. The customer actual recorded variations in reject rate that were time dependent based on these test floor temperature variations.
Process Technology
The impact that process technology had on the ADC performance is counterintuitive. It was not the inherently higher noise or faster MCU speed in the smaller process technology that led to the increase in reject rate. It was an unintended consequence of the higher speed MCU. The design engineer was instructed to upgrade to a faster MCU to add more filtering to improve the accuracy of the system. The problem was that more filtering introduced 1/f noise, which increased the noise and the reject rate.
It is important to note how digital techniques can be used to improve analog performance. The accuracy of the system can be improved by using digital calibration techniques. The precision of the system can be improved by using digital techniques such as averaging. However, there is a limit to how much precision can be improved due to 1/f noise and drift. As parameters start to drift, the impact of the drift negates the improvement from digital techniques.
How did the customer resolve the issue? The customer determined that the key DC specifications that impacted accuracy were: INL, DNL, offset, offset drift, gain, and gain drift.
Surprisingly the only parameters that were specified in the device they were using were offset and gain. Ultimately the customer chose to use a standalone ADC, which fully specified all DC parameters over temperature. Furthermore, they were able to reduce the digital filtering requirements in their MCU which reduced the processing speed needed by their system. Their reject rate and test variation dropped dramatically and their product quality improved.
When evaluating devices for analog performance it is important to understand the difference between precision and accuracy. If you only need repeatability in your measurement, then parameters that specify precision matter. If you need your measurements to match or meet an expected value or time and temperature, then accuracy matters.
To read the previous articles on this matter: