Learn About Current and Voltage Transitions
With the transition from the internal combustion engine (ICE) to electric propulsion accelerating, the resulting and required technology transitions need to be evaluated.
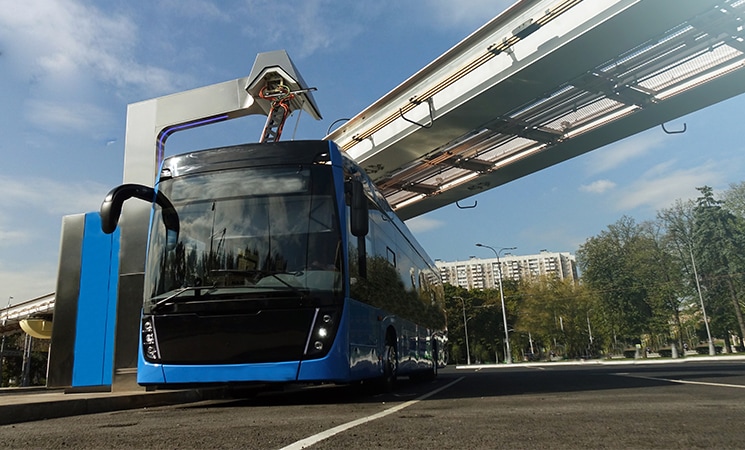
The high power, high voltage requirements of electric vehicles (EVs) of all types, including electric buses and other e-transportation power systems, require the higher efficiency of silicon carbide (SiC) technology to replace older silicon FETs and IGBTs. Safely and efficiently driving these more efficient SiC devices can occur with digital instead of analog gate drivers and many non-automotive or off-vehicle applications will benefit.
EV Projections Accelerating for Automotive
Improved battery technologies, decreasing battery manufacturing cost and governmental targets for reduced CO2 emissions have accelerated the conversion to full electric vehicles. According to Yole Développement, the EV/ hybrid electric vehicle (HEV) market will surpass 41 million vehicles in 2026 and experience a compound annual growth rate (CAGR) of 35%. This means an accelerated transition from gas-consuming ICE vehicles to cleaner EVs.
As a result of the EV growth, Yole predicts that power silicon carbide (SiC) devices in EV/HEV power control and conversion are poised to grow beyond US$1.5 Billion in 2025 with a CAGR of 29%. SiC power devices and the improved battery technologies can be used in other vehicles, such as electric trains, buses, off-road and other e-mobility vehicles, as well as off-vehicle charging and other non-automotive applications that will benefit from automotive EV growth.
The SiC Power Transition
As a wide bandgap material, SiC has a strong physical bond that provides high mechanical, chemical and thermal stability and can be used at higher junction temperatures than silicon.
One of the design tradeoffs is the turn off time for a SiC MOSFET, which is extremely short. When the turnoff rate is high, a high di/dt can cause severe voltage spikes. Other challenges include noise, short circuits, overvoltage and overheating. While this complicates the design of a gate driver, a well-designed gate driver can further reduce losses and simplify SiC implementation and design-in.
Driving SiC Gates
Traditional analog gate drivers are slow for SiC’s response time requirements and difficult to modify for desired operation and performance. In contrast, a digital gate driver, or gate driver core, can solve these issues and address noise, short circuits, overvoltage, overheating and other design problems as well. Microchip’s AgileSwitch® 2ASC-12A2HP, a production-qualified 1200V digital gate driver, allows designers to safely and reliably drive SiC MOSFETs. The driver’s software configurable Augmented Switching™ technology offers multiple levels of control and protection to ensure safe, reliable operation.
The gate driver has two independent operating modes to provide highly efficient normal operation and safe shut-down in the event of a fault, and each are configurable. Normal Operation can be optimized for the best performance of voltage overshoot and switching loss. When triggered, Fault Operation turns the device off quickly and safely. While sacrificing some switching loss, this process, saves the device from catastrophic failure.
Make vs. Buy: an Easy Transition
While many designers are confident designing drivers for Si IGBTs, SiC drivers present problems. For new SiC designs, especially those migrating from IGBT-based converters, the learning curve is sharp, expensive and lengthy. The digital gate driver board with available design tools minimizes the learning curve and offers a production ready solution.
With the Intelligent Configurable Tool (ICT), designers can change the control parameters of the digital gate driver without picking up a soldering iron. Debugging system-level issues can be very difficult. Using PICT 4 or MPLAB, the performance features in the driver can be reconfigure while it is in the application, simplifying the design and expediting development time.
Most analog gate drivers cannot pin-point the location of a fault. With the ICT, the new Digital Gate Driver can. The software tool allows users to turn faults on or off at a variety of checkpoints to focus on the problem.
More Development Tools
Compatible with a variety of Microchip SiC modules using Reference Module Adapter Boards, the gate driver core also has an Augmented Switching Accelerated Development Kit (ASDAK) that includes gate drivers, module adapter boards, a programming kit and the ICT software for silicon carbide MOSFET modules.
A Qualified Solution
The production-qualified gate drivers meet stringent transportation industry requirements including mean time between failures (MTBF), shock & vibration, and temperature cycling.
Towards Cleaner, Safer and More Efficient Driving
For e-transportation applications that require high power (20 kW and higher) and voltages up to 1.2 kV, SiC devices with digital gate drivers provide the efficiency edge. This means that EV propulsion, conversion and charging applications in a variety of applications, including buses, trucks, trolleys, heavy duty vehicles, trains and their infrastructures can benefit from this new design approach. Microchip’s AgileSwitch 2ASC-12A2HP dual-channel, digital gate driver opens these possibilities and provides a simplified, safe and reduced time to market solution.